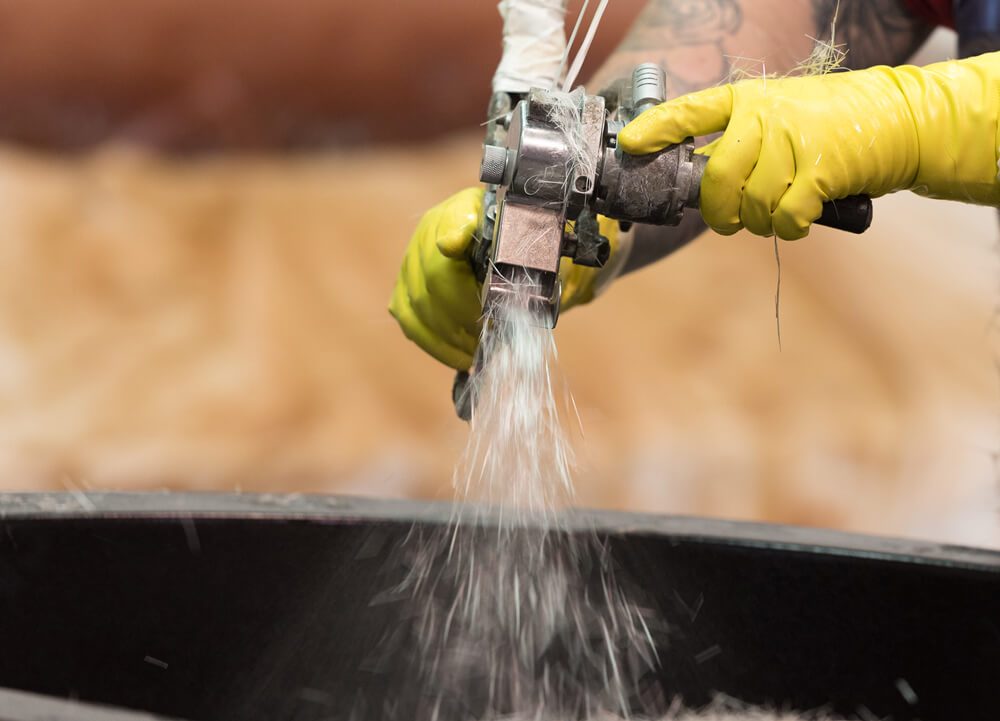
Composites
National Manufacturing Group excels in advanced composite manufacturing, offering a broad spectrum of techniques including state-of-the-art Robotic Open Mold and traditional methods, along with expertise in Composites – Light Resin Transfer Molding (LRTM), which utilizes a vacuum to draw resin into the mold, and Resin Transfer Molding (RTM), where resin is injected under pressure, ensuring precision and quality in every product. The company’s repertoire also encompasses Liquid Compression Molding (LCM) and Sheet Molding Compound (SMC), complemented by a specialized painting division for a full-service approach to diverse composite applications.
…