National Manufacturing Group Unveils Revolutionary C3 Molding Process
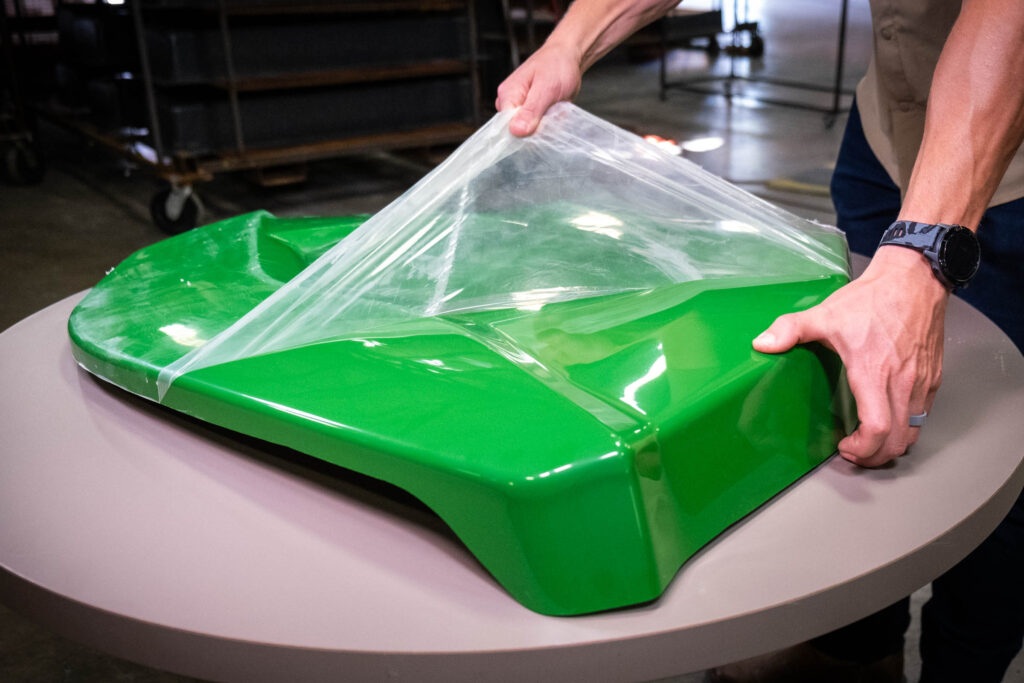
FOR IMMEDIATE RELEASE
National Manufacturing Group Unveils Revolutionary C3 Molding Process
Troy, MI | [October 14, 2024] – National Manufacturing Group is excited to announce the launch of its groundbreaking proprietary molding process, C3 Molding, which stands for Cosmetic Capped Compression Molding. This innovative technology is set to revolutionize the industry by delivering superior parts cosmetically, mechanically, and financially.
Introducing C3 Molding: A Game Changer
Adam Fenton, CEO of National states, “We’ve harnessed our diverse capabilities to develop C3 Molding, a process that merges the surface aesthetics and cost effectiveness of thermoplastics with the versatility and strength of fiberglass. This unique approach also benefits from the rapid cycle times of compression molding.”
Key Benefits of C3 Molding:
- Superior Cosmetics:
- The thermoplastic cap offers options such as high gloss capped ABS for exceptional UV protection and weather resistance, ideal for exterior applications.
- For interior applications, a textured low gloss material is available, all featuring a molded-in protective film to prevent minor shipping and handling damage.
- Material Versatility and Strength:
- Reinforced with fiberglass, C3 Molding allows for various lamination schedules to meet specific mechanical requirements.
- Easily molds in reinforcement ribs and bosses for mounting, providing a smooth B-side finish.
- Achieves up to a 50% fill ratio in the resin, catering to FST requirements and heat management.
- Enhanced Surface Protection:
- The cap ABS surface delivers excellent scratch, mar, and impact resistance, superior to traditional gel coat or paint finishes.
- Minor repairs are effortlessly addressed with a quick polish and buff.
- Cost Efficiency:
- With up to a 50% resin fill ratio, material costs are significantly reduced.
- A 5 to 10-minute cycle time ensures rapid production of molded, finished parts, vastly quicker than other fiberglass molding processes.
- Eliminates the need for spray, finish and cure times associated with paint and gel coat, leading to substantial cost savings.
- Offers up to a 50% reduction in part price compared to light RTM with a painted surface.
- Tooling Expense Reduction:
- Utilizes composite tooling, which costs about half as much as traditional steel compression tooling.
- A single tool set with the C3 Molding process can produce upwards of 10,000 units per year.
A Commitment to Innovation
“At National Manufacturing Group, we are dedicated to pushing the boundaries of innovation. With C3 Molding, we are not just offering a new product; we are delivering a solution that enhances performance, efficiency, and cost-effectiveness. We look forward to seeing how C3 Molding can transform your next project,” adds Adam Fenton. For more information, view our video at bit.ly/C3Molding.